The studied system is an automotive part developed by Punch Powertrain. Its function is to provide a given power to an electric car. More precisely, this part possesses several electric power components. By providing power to the car, the electronic components will heat and are likely to deteriorate and damage the nearby components. The principle is to use a coolant circulating in a pipe situated under the plate (in grey) on which the power components are disposed. This heat-carrying fluid aims at exchanging the heat/energy through the plate on which the components are attached and at cooling them.
A CFD study makes it possible to observe the temperature that the components will reach as well as the load losses indicating an energy dissipation in the system. To compensate the load losses and maintain the flow, the pump will require more energy from the car, hence the necessity of reducing the losses.
The point of the CFD simulation provided by Phimeca is to get an expertise from engineers specialized in fluid mechanics in order to ensure that the electronic components observe the maximal permissible temperature when the car is running.
Thermal transfers
The temperature difference lowers gradually between the fluid and the components, the fluid heats itself and extracts less calories. The liquid is clearly hotter at the end of the pipe thus, it exchanges less heat with the components that are close to the output.
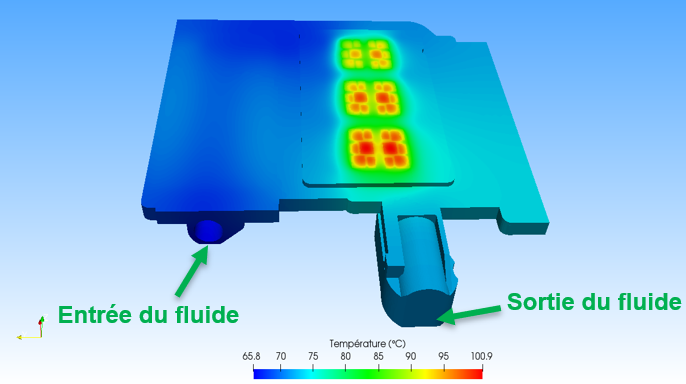
Streamlines and recirculation zones
The pipe abrupt bend generates a boundary layer separation and thus, a recirculation zone. This is a “dead” zone where the liquid slows down and goes in chaotic directions. The whirlpools appearance produces frictions that causes load losses.
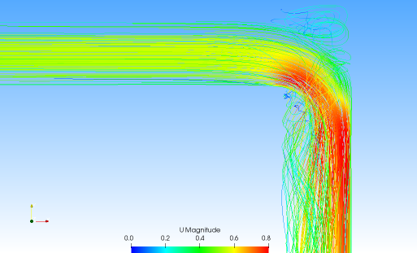
Load losses
It is important to be able to quantify the load losses in the system in order to evaluate its energy performances. If they are too important, different shape optimizations may be provided, for instance, to bow the bend shape so that the latter is less abrupt.
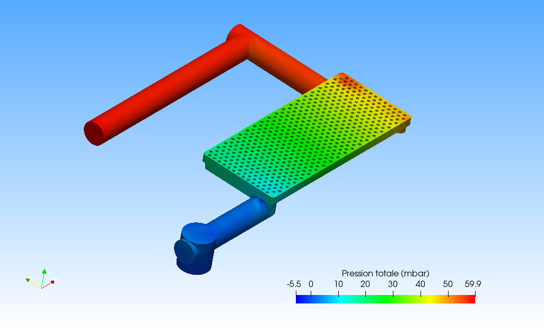